Review of the Zurich Logistics Colloquium: Experiences and Trends from the Field
The 37th Zurich Logistics Colloquium was a complete success. The 2022 edition, organized by Dr. Acél & Partner AG in collaboration with ETH Zurich, Institute for Machine Tools and Production IWF, showed with its lighthouse projects "New Level Operations": The future is digital!
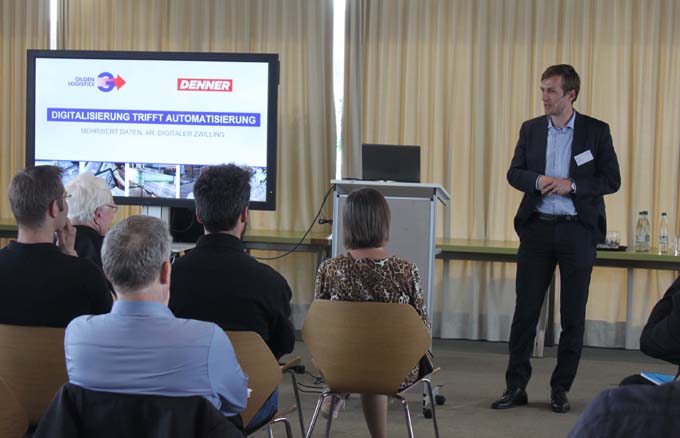
On Tuesday, May 10, 2022, the Zurich Logistics Colloquium could be held again in the Lecturers' Foyer of ETH Zurich after a two-year "Covid-19"-related break. Around 70 guests took the opportunity for a lively exchange of ideas in the course of the four presentations. Afterwards, a view of a beautiful sunset over the city of Zurich was not to be missed.
"No mechanical engineering without logistics
Frank Brinken, Chairman and Founder of BB Intec AG in Rotkreuz and holder of various supervisory and administrative board mandates, postulated "No mechanical engineering without logistics". He impressively illustrated that machine tools are the mother of all machines. Without machine tools, there would be no industrial products. Europe has the largest world market share (35%) in the production of machine tools with a turnover of around 28 billion. Euro (2019). Brinken makes it clear that for such machines with up to 12,000 individual parts, not only good and long-term supplier relationships are needed, but also a large pre-financing requirement must be ensured. The variety demanded by customers results from the combination of basic machines with various components and specific assemblies. In product development; e.g. also through "design-to-shipment", transport costs and time can be saved. For quality components, there are only three global clusters worldwide: Europe with Italy, southern Germany, the Czech Republic and Switzerland, Taiwan and Japan. To date, the mechanical engineering sector has been largely spared the current crises. But those who are already tackling the three biggest challenges in Europe today, such as the dilemma of small batch sizes, sourcing and transport costs, are well equipped for the future, Brinken sums up.
How to reduce the inventory value
Dr. Gesine Moritz, Division Manager Supply Chain Management and Member of the Executive Board of Woodpecker AG Frauenfeld, followed with her insight on "Change in Retail". She pictorially showed the way of Woodpecker AG from distributed local dealers to a future-oriented and successful process-oriented sales organization. In the process, logistics was the decisive success factor. Service levels were developed and implemented. For example, new customer orders received by 5:00 p.m. are guaranteed to be delivered the following day. Inventory value has been reduced by over 20% in three years and inventory turnover has increased from 2.5 to 4.5. The biggest stumbling blocks in this transformation were also the biggest success factors: WE the people. Regular communication with employees, involvement from the outset according to the motto "turn those affected into participants," trust and empowerment, and letting brakemen off the hook proved particularly effective.
Digitalization meets automation
The future is digital! This was impressively demonstrated by Daniel Gilgen, Deputy CEO and Business Unit Manager Systems at Gilgen Logistics AG Oberwangen, on the topic of "Digitalization meets automation". Gilgen gave an in-depth insight into the implementation of seamless data continuity throughout the entire life cycle of logistics systems. The innovative solution approach of Gilgen Logistics AG links state-of-the-art technologies such as augmented reality, digital twin, cloud server and GS1 Digital Link with customer and manufacturer systems and brings them together with intralogistics. The data can be accessed at any time from anywhere in real time via the cloud. This means that all relevant information is accessible to those involved in the right form. The use of augmented reality in the sales process enables potential customers, for example, to take a virtual tour of the developed plant concept with the option of checking it directly in the virtual world. The first individual digital system went into operation in the fall of 2021 at Denner's distribution center in Lyss. After only a short period of time, increased productivity was already evident for the end customer and suppliers.

Joint research project
This year's Zurich Logistics Colloquium was concluded by Werner Züllig, Head of Technology at Geberit Produktions AG Jona and Prof. Dr. Andreas Kunz, Head of the Innovation Center Virtual Reality at ETH Zurich. They provided insight into exciting results from a joint research project on the topic of "Virtual Reality in Workplace Design". Stable standardized processes are to be used with the Geberit Production System to ensure that manual workplaces can also be improved while avoiding waste of resources. In the joint research project, workplaces were evaluated entirely in the virtual world using the MTM method and potential improvements were identified. The benefits are sustained high cash generation, even for small quantities, as well as operating margins that are significantly above the industry average. Geberit is consciously driving forward this strategic initiative of digitalization and sees it as a major opportunity for genuine value creation at the Swiss site.
Source and further information