Connected Work establishes itself on the store floor
The manufacturing industry is undergoing a transformation, as digitization is increasingly reaching frontline employees in manufacturing companies. Under the buzzword "Connected Work," they too are expected to benefit from full digital connectivity with their work environment. But in many companies, digital tools are still competing with mountains of paper - inefficient, costly media disruptions are the order of the day. With the [...]
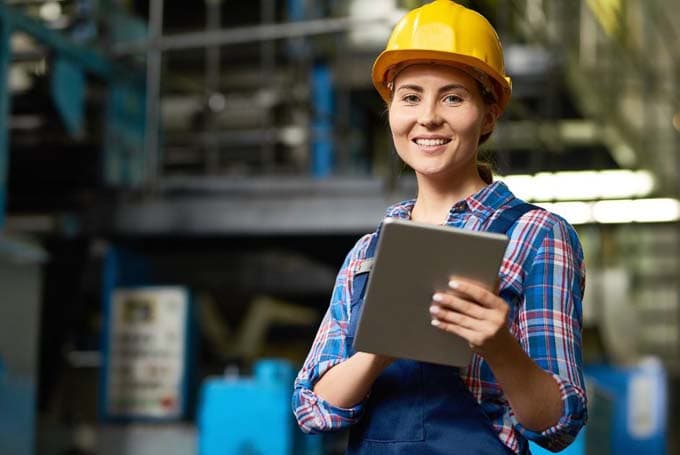
The manufacturing industry is undergoing a transformation, as digitization is increasingly reaching frontline employees in manufacturing companies. Under the buzzword "Connected Work," they too are expected to benefit from full digital connectivity with their work environment. But in many companies, digital tools are still competing with mountains of paper - inefficient, costly media disruptions are the order of the day.
With the Connected Work Study 2023, the software company Operations1 wanted to shed more light on the topic of "connected work in production". To this end, the company surveyed a total of 175 specialists from the production environment on the status quo, the future of Connected Work and the necessary implementation measures. The results are some significant and surprising findings that were presented to the public at the end of February 2023.
Only 3 % of the companies surveyed work paperless to date
Paper has played a central role in the production environment since the beginning of industrialization: from the provision of order papers to the safeguarding of process knowledge to the documentation of quality findings, labeled or printed sheets play a major role. And even more than 10 years after the term "Industry 4.0" was defined, it is still in use everywhere. Although there is much more to the concept of Connected Work than the mere digitization of paper documents, the responses of those surveyed show that Connected Work, while increasingly important, is far from having become a mass phenomenon: Only 3 % of the companies surveyed stated that they have worked completely paperless to date, while 18 % work exclusively with paper-based processes. 17 % describe themselves as largely paperless and 62 % are still partially so.
Although the majority of respondents still work in a paper-based manner, there is a consensus that paper is no longer an up-to-date relic in the age of digitization. The study participants associate a number of operational challenges with paper-based working methods: The three biggest issues are the time-consuming creation and updating of documents (44 %), data procurement, interpretation efforts and archiving (34 %), and non-value-added activities such as manual data transfer (29 %).
In each case, the entire production chain is affected by paper-based processes: From the provision and training of knowledge, through the execution of activities, to the documentation and evaluation of information. A decisive reason to say goodbye to paper as quickly as possible is the associated savings potential: the costs of paper management are in the five-digit range for 25 % of the respondents, and for 5 % even more than €200,000 per year. "Companies initially see creation effort and paper costs as key reasons for moving toward Connected Work. But deeper conversations quickly identify opportunities for six- to seven-figure savings potential through the introduction of intuitive, seamless processes on the store floor," explains Benjamin Brockmann, CEO and Co-Founder of Operations1.
The future is "connected
The majority of respondents have recognized the potential to make processes more effective and drastically reduce cost points with Connected Work. 69 % see Connected Work as the future. At 59 % of the participants, corresponding initiatives are already being driven forward in the company. 21 % of the respondents even stated that they have a Connected Work officer who is specifically dedicated to this topic. Nevertheless, the opinion picture is not uniform, as 26 % do not yet see any initiatives in the area of Connected Work in their company.
The study results underscore that although Connected Work is not yet a mass phenomenon, it is increasingly establishing itself strongly on the store floor. This is a new development, as operational employees in production, logistics and other production-related support processes have long been neglected in digitization. In recent years, there has been a growing trend to equip even the "deskless" employees with digital technologies and to better network them within the organization. This networking will significantly change the manufacturing industry in the coming years. "For the path to Connected Work to succeed in the long term, it is important to be constantly open and curious about the changes that connected work brings. Only in this way can we all derive maximum benefit from the numerous possibilities and opportunities that the manufacturing industry will be presented with," says Brockmann.
Study results briefly summarized
- While 18 % work purely paper-based, 3 % of the respondents stated that they are already completely paperless. 17 % describe themselves as largely paperless and as many as 62 % are already partially so.
- Connected Work is not yet an established mass phenomenon, but about 70% of the participants see it as a future field and 21% have already created a specialized role for it in their company.
- The field of activity of operational employees will change significantly in the next 20 years: From standard to non-standard activities. At the same time, this will entail a rethinking of how employees can be supported digitally in the best possible way in the future.
- In the target picture, study participants see mobile apps as leading technologies for empowering employees. According to the respondents, the greatest potential of Connected Work lies in productivity increases, easier document creation and updating, securing process knowledge, and shortening response times for problem resolution.
- When implementing Connected Work, it is essential to take a systematic approach that involves operational employees in a far-sighted manner. The key success factor here is good communication.
Source: www.operations1.com
This article originally appeared on m-q.ch - https://www.m-q.ch/de/connected-work-etabliert-sich-auf-dem-shopfloor/