Modular room systems as a sustainable solution for urban development
Whether an office extension, a hospital extension or additional space in a public building such as a school - cities are growing and need structural solutions that can be implemented quickly and flexibly. Modular room systems offer clear advantages over conventional construction methods such as timber or concrete thanks to their modular design. In addition to the desired properties - speed and flexibility - they are also more ecological and economical.
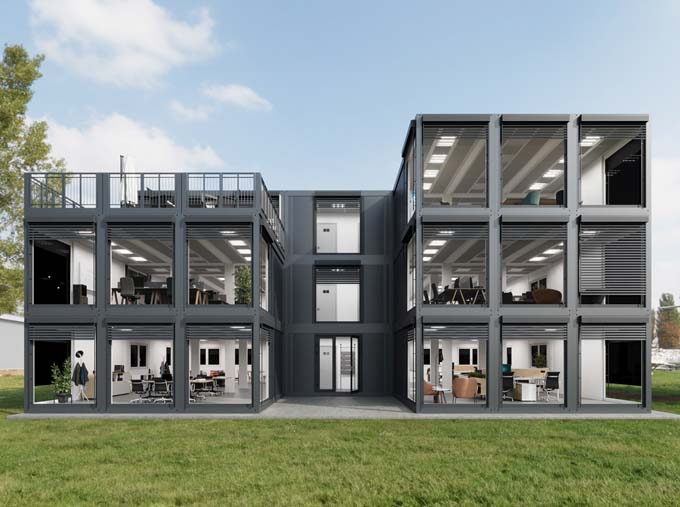
From the countryside to the city - according to Statista, around 85 percent of the Swiss population already live in cities[1]and the trend is rising slightly. If more people arrive or their needs change, additional space quickly becomes necessary: Housing, commercial space, public or cultural and leisure buildings. However, this rapid growth presents cities with major challenges and often comes at the expense of infrastructure. Building new roads and bridges, developing the sewage system and laying data lines, for example, is difficult to accomplish under time pressure.
Constructing buildings in the traditional way also usually does not meet the required speed due to its sequential approach: long planning phases, environmental preparations, construction of foundations and basements take a lot of time before walls are finally raised, rooms are developed and made ready for occupancy. In addition, traditional construction methods do not meet the flexibility required in the context of growth. This is because the need for additional office or commercial space, for example, can change or even disappear over the course of the building's life cycle. If the building complex is then built conventionally, the excess capacity remains empty and cannot be demolished or can only be demolished at great expense.
Flexible use according to space requirements
However, the situation is different with a modular design: It is flexible, can react to changing requirements and can be implemented quickly. This is because it relies on individual prefabricated polyvalent or steel modules, for example, which are combined in a modular system to form the entire building structure. Each module corresponds to a planning unit that can have a ceiling, walls, windows, floors, doors and installations. How the module is prefabricated is decided by the client at the start of the construction project, depending on the purpose - bathroom, kitchen, office, living room, etc. How the individual room units are arranged to form a building is also determined in advance by the planner and then realized in the factory. In this way, a house is created within a very short time, which can be added to or taken apart and reduced in size again during the course of the building's life cycle, depending on the space required. It is also very easy to remove entire layers or floors. It is also possible to relocate the modules by separating them from each other, transporting them to the new location and reassembling them there.
Speed ensures rapid feasibility
However, it is not only the flexibility of the construction method that makes it suitable for the rapid urban growth, but also the immense time savings in the realization of construction and dismantling. As the modules are delivered prefabricated from the factory, delivery and assembly usually take place within a few days. Long planning periods can be dispensed with and work takes place in parallel. Whereas in a traditional construction method, planning takes place first and then one trade follows the next on the construction site, in the factory, for example, work on the foundations of the individual modules can be carried out in parallel with the design of the room program; structural issues are eliminated - as the system is structurally coordinated. In addition, modular construction eliminates the need to search for different trades or wait for individual trades - well-established resources already take care of this during production:
As there is also a shortage of skilled workers in the construction industry, it has sometimes become difficult for builders to order all trades to the construction site at the right time, which often leads to delays. The problem of having to synchronize these trades with each other on the construction site does not arise with modular construction: All tradesmen involved in the construction of the modules are directly available in the factory. There are also far fewer interface or communication problems, as the workers are familiar with each other and are used to working hand in hand.
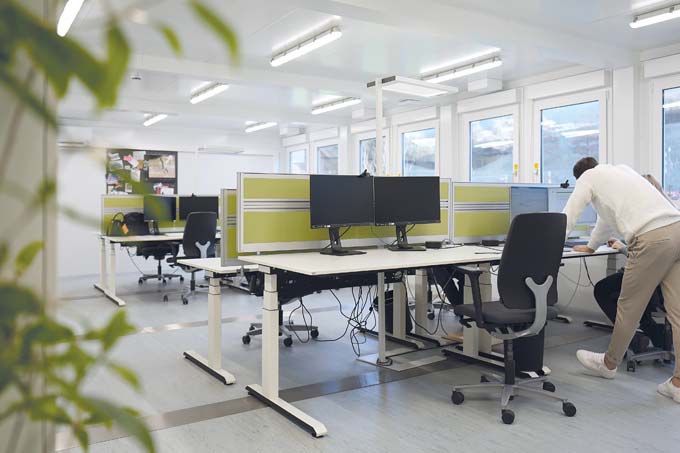
Ground screws provide a fast, flexible and sustainable basis for modular construction
Another important factor for the high implementation speed of modular room systems is the foundation. In principle, the foundations are laid in parallel with the module production, thus generating synergies in the construction process. In particular, screw foundations are an innovative solution that are characterized by the fact that they can be installed without extensive earthworks compared to traditional concrete foundations. This enables immediate load-bearing capacity and shortens the construction time, as there is no curing time for concrete foundations. Energy-intensive concrete production is therefore not necessary, which reduces the consumption of resources. In addition, screw foundations can be removed without leaving any residue or reused at another location as required.
As there is no need for time-consuming foundation work and the modules are placed directly on the prepared screw foundations, building owners also benefit from significant cost savings. The screw foundations in particular therefore prove to be an economic and sustainability driver.
More ecological and economical than conventional construction methods
In addition to speed, modular room systems also score points for their CO2-balance sheet. In general, it can be said that modular construction enables material savings of 30 to 60 percent compared to conventional construction methods. This is because using less material also means a reduction in CO2-emissions. Another example of this is the use of concrete: worldwide, concrete construction is one of the biggest CO2-producers, since the chemical combination of water and cement produces CO2 is released. As significantly less concrete is used to manufacture the modules, this improves the CO2-balance of modular construction compared to traditional buildings to a considerable extent.
Furthermore, the CO2-footprint alone thanks to the modular design principle. As modules can be used variably and can be dismantled or rebuilt as required, finished rooms are often ready for use again after one use. This means that rooms produced once can be used several times, so that no new rooms need to be built. This also has a positive effect on the CO2-reduction compared to a classic design. In addition, modules that can no longer be used are largely recyclable: Steel, mineral wool and glass, for example, are materials that can be melted down and reused after use.
Resource-conserving production, multiple use and recyclability show that modular room systems are fully in line with a sustainable circular economy. The aim is to use the resources required and the products produced as ecologically and economically as possible. At the same time, this creates efficiency effects: The production costs of modular construction are 35 to 40 percent lower per square meter than wood or concrete construction, for example. This means that modular construction is not only more ecologically sustainable, but also more economical.
Best practice for the Circular economy
For leading suppliers of modular room systems such as Condecta in particular, sustainability is therefore turning from a buzzword into a lived practice. The use of resource-saving solutions, reusability and recyclability as well as the environmental efficiency of the modules must take center stage in the face of climatic challenges. To this end, the modular buildings are designed in such a way that they fulfill key aspects of the circular economy, for example by using durable materials in particular to reduce the environmental impact.
Providers such as Condecta also minimize the ecological footprint during the construction process itself: production in a controlled industrial environment generates less waste than on traditional construction sites, and the need for energy-intensive materials is drastically reduced. This actively contributes to promoting sustainable building concepts and helping to shape the transition to resource-saving, climate-friendly construction methods.
Modular construction: Particularly attractive for cities
As temporary solutions, modular space systems are particularly attractive for cities. For example, schools or public buildings often need to be renovated or derelict areas used for a certain period of time until a long-term solution using conventional construction methods has been completed. Modular buildings are a suitable alternative for this temporary transitional period, as the modules can be constructed both horizontally and vertically. They also offer a wide range of possible uses, for example as a classroom, office, store or canteen or as premises in a social facility, meaning that modular construction can cover the required areas of application depending on the case. If additional space is required at a later date, this can be done with minimal disruption to traffic and minimal additional effort - a crane can add up to ten modules in half a day, for example.
Conclusion
Modular space systems are the ideal solution for growing cities: they are flexible in every respect - in their use, their temporary use, their adaptation to space requirements and even in the event of a change of location. They can be realized more quickly and, thanks to their circular economy approach, are more ecologically and economically sustainable than conventional construction methods. Especially in cities where space is limited, vertical modular construction is an attractive solution - and it can be adapted to changing space requirements at any time.
[1] https://de.statista.com/statistik/daten/studie/216770/umfrage/urbanisierung-in-der-schweiz/
Author: Vicente Raurich is Head of Project Business at Condecta AG. The company is a leading provider of innovative solutions in the areas of modular room systems, construction logistics and event infrastructure. www.condecta.ch