Manufacturing: Six investments that pay off in times of crisis
The threat of recession, high energy costs, supply chain problems, a shortage of skilled workers - many companies are facing numerous challenges. The economic outlook is bleak; economic researchers at the ETH are forecasting GDP growth of 1.2% for Switzerland. In Germany, our country's most important trading partner, economic experts expect growth to be even lower.
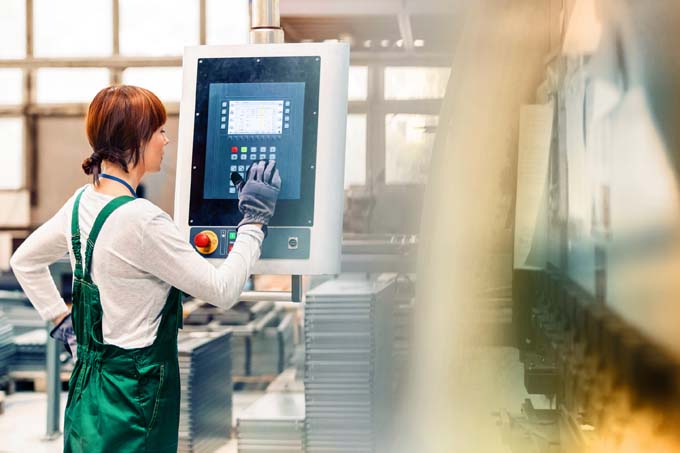
Even if demand is falling and cost pressure is increasing, manufacturers should not put planned projects on hold. After all, new technologies in particular can help during the crisis and the time afterwards. At least that's the belief at software and hardware manufacturer Oracle, which has outlined six ways in which companies can get through the crisis.
1. digitization and data analytics
The digitalization of production, procurement, supply chain and manufacturing processes is creating smart factories that are further accelerated by the Internet of Things (IoT), artificial intelligence (AI) and machine learning (ML). The basic idea: analyzing large amounts of data improves decision-making. According to a Survey by Deloitte in 2013, 60 percent of managers were already using analysis software, often with AI functions, to identify component bottlenecks in good time, optimize delivery routes, reduce fuel consumption and shorten delivery times.
2. reduction of supply chain risks
Geopolitical and trade tensions are prompting more and more companies to look for lower-risk suppliers. According to a Study by BCI Global more than 60 percent of European and US manufacturers are planning to relocate some of their activities to Asia in the coming years. Some EU companies also have their sights set on the Czech Republic, Poland and Hungary - others on Germany, the Netherlands, Belgium and Luxembourg.
Modern supply chain technologies can also help to reduce supply chain risks. Better insights into workflows, schedules and capacities, fleets and distribution warehouses, as well as real-time status updates, enable companies to quickly identify and resolve bottlenecks. ML capabilities highlight anomalies and potential impacts. In a Study by KPMG 67 percent of CEOs stated that they want to invest more in data-driven technologies.
3. smart manufacturing
Manufacturers are using Industry 4.0 technologies to optimize production processes, improve product quality and automate maintenance. Typical examples include drones that detect structural damage to factory equipment, robots and cobots as well as cloud applications for automated demand planning. Digital twins simulate the effects of fluctuations in supply and demand on assembly line production. Augmented reality (AR) speeds up repairs and 3D printing enables the production of missing spare parts. Driverless vehicles deliver components to the assembly lines via the 5G network. Intelligent warehouses monitor stock levels and independently request parts.
According to ABI Research global spending on automation technologies will increase from 345 billion US dollars in 2021 to over 950 billion US dollars in 2030. Automotive manufacturers in particular are investing in solutions to reduce labor costs and increase safety and productivity. In 2022, the automotive industry will account for more than half of robot sales. Overall, the global market for industrial robots is expected to grow by Grand View Research will grow by an average of 10.5 percent per year until 2030.
4. qualified tech specialists
The manufacturing industry is also affected by the shortage of skilled workers. There is a shortage of assembly line workers, welders, machine operators, industrial mechanics and production managers. Due to the increased use of new technologies, the industry also needs specialists in the fields of robotics, programming, integration of intelligent systems, prototyping and cyber security as well as data scientists.
Real-time information is the prerequisite for the digital networking of all employees. So-called Connected Frontline Workforce (CFW) applications can alleviate the shortage of skilled workers. Training and further education is also important - for example, the European Commission's workshops, which are specifically aimed at the manufacturing industry. And recruiting applications in the cloud make it easier to fill technical positions in highly competitive markets.
5. anything-as-a-service
More and more companies are offering their products or their ongoing maintenance, monitoring or installation as a service. A manufacturer of welding robots, for example, takes on a certain number of welding jobs for a fee instead of selling its robots. This revenue is easier to plan than sales revenue. Anything/Everything-as-a-Service also offers additional cross-selling and upselling opportunities. Analyses from Accenture According to the company, this model can increase sales by 15 to 20 percent annually. According to Fortune Business Insights from USD 545.35 billion in 2022 to more than USD 2.3 trillion in 2029.
More and more car manufacturers are also opting for the subscription model and offering registration, taxes, insurance, breakdown assistance and maintenance as services. According to Global Market Insights the global Vehicle-as-a-Service market is expected to grow to 30 billion US dollars by 2030.
6. sustainability
A quarter to a third of the world's energy is used for manufacturing processes. Manufacturers' supply chains in particular have a negative impact on the environment - for example during the extraction, production, transportation and storage of raw materials. The industry is under massive pressure to become more environmentally friendly and sustainable. Most companies are aware of this, as a survey by Harris Poll shows. According to the survey, 56% are taking measures to operate more sustainably - the highest proportion of all industries surveyed.
New tools are also being used. Blockchain, for example, makes it easier to trace materials and goods. Automation and monitoring solutions provide detailed insights into production processes, supply chains and energy consumption. This helps manufacturers to increase their productivity and identify potential savings.
Conclusion: Do not forego investments in a weak economy
"Even a weakening economy shouldn't stop companies from investing in new technologies," explains Martin Cereceda, Senior Business Development Manager Manufacturing & Automotive at Oracle. "On the contrary: those who digitize, automate and take an environmentally friendly approach will gain a competitive advantage - in the form of efficient business processes, innovations and long-term cost reductions."
Source: Oracle
This article originally appeared on m-q.ch - https://www.m-q.ch/de/fertigung-sechs-investitionen-die-sich-in-krisenzeiten-rechnen/